[공구 노트] 절삭 가공 계산식 및 자주 사용하는 용어 정리
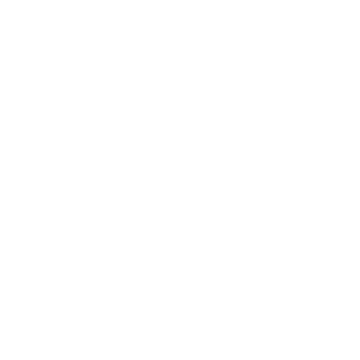
안녕하세요. YoungH입니다.
오늘은 금속 절삭 가공 시 사용되는 계산식 및 자주 사용하는 용어의 정의에 대해 알아보겠습니다.
금속 절삭 가공 계산식
▶ae : 직경 방향 절삭
▶ap : 축 방향 절삭
▶ar : 직경 방향 절삭(사이트 커터용)
▶Dap : 절삭의 공구 직경
▶Dc : 공구 직경
▶Dm : 가공 직경-절삭
▶fn : 1회전당 이송
▶fz : 1날당 이송
▶hm : 평균 칩 두께
▶kc : 비 절삭 저항
▶lm : 가공 길이
▶n : 스핀들 속도(rpm)
▶Mc : 토크 값
▶Pc : 정미 동력
▶Q : 칩 배출량
▶Vc : 절삭 속도
▶Ve: 경제 절삭 속도
▶Vf : 1분당 이송
▶Zc : 공구 유효 날 수
▶Zn : 공구의 날 수
계산식은 상기 표의 우측 공식을 참고하자.
금속 절삭 가공 용어 정리 및 정의
▶이송 속도 : 드릴 등의 공구가 피삭재에 홀을 뚫는 속도로 단위는 Vf로 나타낸다.
▶칩(부스러기) : 절삭한 뒤 피삭재에서 발생하는 절삭 찌꺼기, 안전하고 효율적으로 작업하기 위해서는 최적 칩 브레이커 형상을 가진 절삭 날을 준비하여 칩을 잘 배출해야 한다.
▶칩 처리 성능 : 절삭으로 발생하는 칩을 처리하는 성능이다. 공구가 피삭재로 빠르게 진행하면 절삭 효율은 올라가지만, 칩은 단시간에 많이 발생하여 칩 처리 성능은 내려간다.
▶절삭 : 피삭재로 공구가 파고 들어가는 깊이다. 깊으면 가공 효율은 좋아지지만 절삭 저항이 올라가서 공구가 손상되기 쉬워진다.
▶절삭 날 : 절삭 공구 본체(바이트)의 앞에 부착된 날이다. 절삭 내용에 따라 형상, 사이즈, 선단 각도, 칩 브레이커, 재질 등을 선택할 수 있다.
▶연삭 가공 : 고속으로 회전하는 연삭숫돌을 이용하여 그 숫돌을 구성하는 대단히 단단하고 미세한 연마 입자로 가공물을 깎아내 가는 가공법이다. 연삭 가공은 고정밀도의 가공이 가능하므로 생산 가공에서 최종 공정이나 마감 가공으로 중요한 역할을 하고 있다.
▶공구 수명 : 공구의 기능을 유효하게 사용할 수 있는 기간이다. 공구 회전수가 높으면 높을수록 공구 바깥 둘레 부근의 실제 절삭 속도도 높아지고 공구 수명은 짧아진다.
▶CNC 선반 : Computerized Numerically Controlled 선반의 약칭이다. 공구의 동작, 절삭 조건의 지정을 컴퓨터로 실행하는 선반 장치로 직선만이 아닌 자유로운 절삭 곡선을 설정할 수 있어 보다 최적의 절삭 가공을 할 수 있다.
▶하단 홀 : 나사 자국을 만들기 전에 뚫는 홀이다. 금속판을 관통하는 「관통 홀」과 빠져나가지 않는 「고정 홀」 등 2종류가 있다.
▶인성 : 금속의 강도, 인성이 높은 금속은 강인하여 내충격성이 우수하고 잘 파단되지 않는 특성이 있다. 인성은 최대 응력 ×최대 변형으로 나타낸다.
▶스터브 드릴 : NC기 등으로 얕은 홀을 뚫을 때 사용하는 짧은 쇼트 드릴이다.홈 길이는 드릴 직경의 3배 이하다.
▶스핀들 : 공작 기계에서 공구를 회전시키는 축=주축부이다. 초고속·고정밀도 절삭이 요구되는 고속 밀링 가공에는 고속 회전이 가능한 스핀들이 불가결하다.
▶스로 어웨이 : 스로 어웨이(Throw away)는 「버리다」라는 의미로 스로 어웨이 드릴(날 끝 교환드릴=일회용 드릴) 등과 같이 사용한다.
▶절삭 속도 : 절삭 시 공구 날 끝이 피삭재에 대해 발생시키는 속도로 일반적으로 절삭 속도가 빠를수록 절삭 온도가 상승한다. 절삭에 악영향을 미치지 않는 범위 내에서 최대한 빠르게 하는 편이 효율이 좋다.
▶절삭 저항 : 절삭 공구에 걸리는 반작용으로서의 힘. 이것이 낮아지면 절삭 효율이 올라간다.
▶절삭 열 : 칩과 공구의 접촉면에 온도 상승으로 발생하는 열이다. 칩을 전단하는 에너지, 칩과 공구의 접촉으로 인한 마찰 에너지, 공구 릴리프면과 피삭재의 마찰 에너지로 인해 발생한다.
▶절삭유 : 절삭 시 공구와 피삭재의 접촉부에 주입하는 기름. 칩의 원활한 배출, 날 끝의 냉각, 절삭점의 윤활을 목적으로 사용
▶솔리드 : 「일체형」이라는 의미로 「솔리드 엔드밀」의 경우 절삭 날과 샹크(엔드밀의 손잡이부)가 일체형으로 절삭 날 교환식(스로 어웨이)과는 역으로 마모되면 재연삭해야 한다.
▶칩 브레이커 : 절삭으로 발생한 칩을 적절하게 처리하기 위해 가공된 돌기부의 형상이다. 칩을 컬링하는 등 길이나 방향성을 제어하는 목적이 있다.
▶초경 : 텅스텐 카바이드를 주성분으로 하이스보다도 고온의 경도에 우수하고, 경도와 인성의 균형이 잡혀 있어 주로 고속·고정밀도 홀 가공용 공구로 폭넓게 사용되고 있다.
▶노즈 R : 노즈는 「코」로 선단이라는 의미다. 절삭 날의 선단 코너부의 R(곡면부) 치수로 최대한 큰 R 치수 쪽이 마감면 조도 정밀도가 일정한 면, 공구 수명의 면에서 유리하다.
▶하이스 : 고속도 공구강으로 강 중에서 가장 단단한 재료로 절삭 공구에 주로 이용된다. 초경 합금보다는 부드러운 강도이기 때문에 드릴 가공 등 비교적 저속으로 꺾임, 빠짐 등이 발생하기 쉬운 가공에 사용된다.
▶버니싱 : 버니시(Burnish)는 「닦기, 갈기」라는 의미. 롤러를 사용하여 금속 표면을 눌러서 경면 마감하는 것을 「롤러 버니싱」이라고 하고 볼을 사용하여 금속 표면을 눌러서 경면 마감하는 것을 「볼 버니싱」이라 한다.
▶돌출부 : 절삭 가공했을 때 소재의 절단면이 튀어나온 여분의 돌출 부분이다. 그라인더나 줄을 사용하여 깔끔하게 깎아 제거하는 것을 「돌출부 제거」라고 한다.
▶머시닝 센터 : 다면 절삭 가공이나 다양한 절삭 가공 등 복수의 기능이 있는 CNC(컴퓨터 수치 제어) 공작 기계이다. 자동 운전으로 절삭 가공이 가능하고 안정된 고정밀도·고능률의 절삭 가공을 연속해서 실행할 수 있다.
▶담금질 처리 : 금속 재료를 고온에서 가열한 후 급속하게 냉각하는 열처리로 금속의 경도를 증가하기 위한 작업이다.
▶야금 (야근) : 미립자의 집합체 인 분말을 제조하는 기술 및 분말을 원료로 재료 및 부품을 제조하는 기술의 총칭이다.
▶워크 (피삭재) : 절삭 가공의 대상이 되는 재료(금속)이다.
▶형상 가공 : 주로 엔드밀(볼 엔드밀 또는 필렛 엔드밀)의 R 부위을 이용한 곡면 가공을 말하며, 곡면 모방 가공(Copy Milling)도 이 범주에 포함시킬 수 있다.
▶윤곽(Profile) 가공 : 윤곽 가공은 EDM Wire Cutter를 이용하는 방법 등 여러 가지 방법이 있을 수 있으나, 일반적으로 엔드밀의 옆날을 이용한 윤곽면 가공을 말한다.
▶펜슬(Pencil) 가공 : 형상 가공시 곡면과 곡면의 경계선에서 공구에 갑자기 큰 절삭 부하가 걸리는 것을 방지하기 위해, 각 곡면 경계선 부위의 여유 소재를 윤곽 가공 전에 제거해 주기 위한 가공으로, 엔드밀의 바닥날과 옆날을 동시에 이용하는 곡면 가공의 성격을 가진다.
▶픽 피드(Peak Feed), 또는 피치(Pitch)
형상 가공시 공구 경로 사이 간격을 말한다. 원하는 표면 조도, 사용하는 공구 직경 등에 따라 결정한다.
▶커습 높이(Cusp Height), 또는 스캘럽 높이(Scallop Height)
형상 가공시 공구 경로 사이 간격(피치)에 의해 생기는 조개껍질 형상의 최고점과 최저점의 높이차를 말한다. 공구 직경과 픽 피드량, 가공면의 기울기 등에 의해 결정된다.
'공구노트' 카테고리의 다른 글
[공구 노트] 계측기 온도계와 습도계의 종류와 특징 (0) | 2023.05.16 |
---|---|
[공구 노트] 나사 절삭 가공(태핑 가공) 탭, 나사산 보정 다이스 종류와 특징 (0) | 2023.05.15 |
[공구 노트] 스텝 드릴, 홀 커터의 종류와 특징 (0) | 2023.05.11 |
[공구 노트] 타공가공(드릴링 가공)의 방법과 종류, 시닝의 정의, 카운터 보어의 용도 (0) | 2023.05.10 |
[공구 노트] 밀링가공 방법 및 엔드밀의 특징과 형상 (0) | 2023.05.09 |